Heading in the same direction – but driving different cars
Within an industrial organization, there are four different domains all doing their best to improve manufacturing performance.
“On the business side, you have the people involved in strategy and those involved in operations all striving to boost performance,” explains Alexander Naessens at delaware. “On the strategic side, decisions have to be made on what and how many products to produce where and how. On the operational side, personnel are working to improve processes, reduce scrap, produce more, increase quality, etc. Both strategy & operations need data and tools to support them in taking these decisions – and that’s where IT and OT come in.”
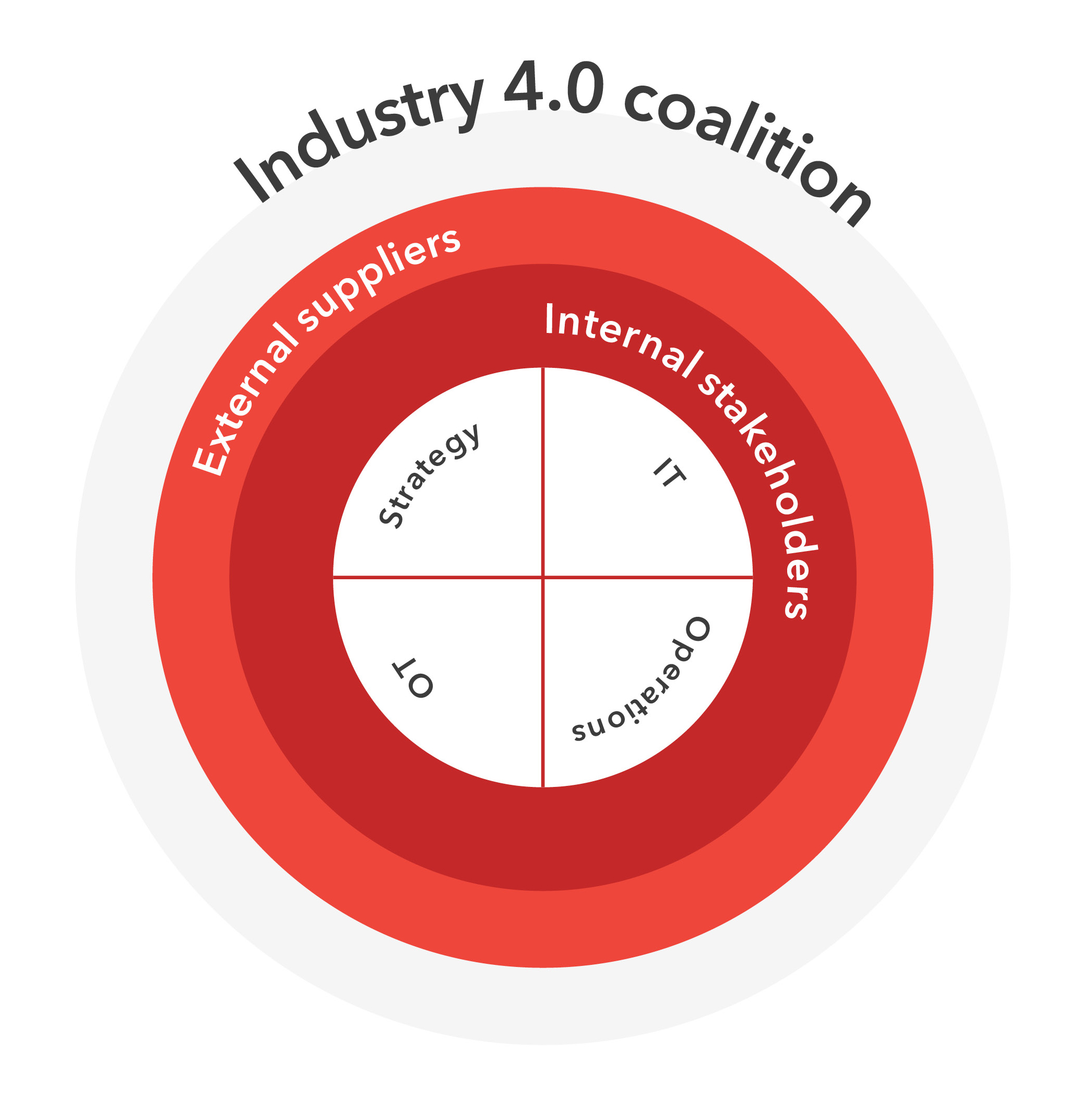
- IT (information technology): tools and functionalities like the ERP, MES and reporting.
- OT (operational technology): robots, machinery controls, screens and devices close to equipment.
“Typically, the IT-solutions are managed by the IT-department, while the OT-solutions, are managed by the engineering department,” Alexander goes on to say. “Sometimes IT and OT offer different solutions to the same business problem – and in many cases they aren’t collaborating very well. The key to really getting Industry 4.0 rolling? Ensuring that IT and OT are on the same page and working together to achieve their shared ambition.”