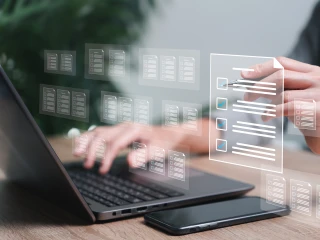
Model takes Quality Management (QM) to the next level
Model Group’s collaboration with Delaware ensures top-quality production through a robust, unified quality management system for all MES solutions.
Model Group’s collaboration with Delaware ensures top-quality production through a robust, unified quality management system for all MES solutions.
The Model Group develops, produces and supplies intelligent, innovative and high-quality display and packaging solutions in solid and corrugated cardboard.
The organisation exists across a wide variety of locations throughout Europe and employs more than 4,200 people in its major markets: Switzerland, Germany, Austria, France, Netherlands, Belgium, Luxembourg, Czech Republic, Poland, Slovakia, Ukraine, Bosnia-Herzegovina, Hungary, Slovenia and Croatia.
Although Model were already using a Manufacturing Execution System (MES) solution, the existing solution lacked both Quality Management (QM) and material flow integration.
The objective of the project was to establish a unified platform for all current and potential new MES solutions across the organisation. The aim of this harmonised process environment was to enable comparability and uniformed KPIs, as well as streamlined reporting.
The initial phase of the project involved the integration of the SAP QM module, which is part of the SAP standard package, into the pre-existing LP.MES solution.
To enable easy operations, a touchscreen-enabled web application based on SAP MII (Manufacturing Integration and Intelligence) and SAP PCo (Plant Connectivity) was then designed, which is available in several languages (DE/FR/EN).
With a functioning software and hardware basis established, the next step was to implement concrete QM processes. In addition to in-process inspections, Model opted to include goods receipt inspections and initial sample inspections, where products are approved by means of a four-eye principle.
The implementation of these individual inspection measures was designed from scratch. As such, the release of the individual orders within production takes place via a checklist, which, like the signature of the inspection itself is processed digitally. This way, inspection points can be filed automatically and trends displayed graphically for analysis - enabling better-informed decision making across the organisation.
The purely digital handling of QM processes brings many advantages. In addition to the simple archiving of production documents and quality checks, it enables totally paperless working. As a result, information about individual production orders is always accessible and can be easily transmitted to various departments across the organisation.
And the best part: the analysis of this data takes place in real-time, meaning it is possible to intervene directly to optimise the existing process - setting Model up for a culture of continuous improvement.
It was an exciting and intensive developing partnership. Thanks to the successful cooperation within the project team and a focus on the common goal, we are now looking at a reliable result.Cornel Müller, Service Delivery and Project Manager ICT Model
By introducing the LP.MES solution based on SAP, Model has taken its QM to the next level. Additional improvements may follow in the future, though.
For example, automatic or optical inspections can be implemented in the production process by using additional hardware such as measuring or camera systems and third-party systems.
Furthermore, LP. and Delaware are working on the next steps towards Industry 4.0 and future innovations for the Model Group on the basis of the LP.MES platform.